When high use swimming pool age, it’s not at all uncommon that structural cracking is going to become an issue. City and public use pools, often indoors, are designed with tile finishes and in many cases, have been installed for decades. There is consistent upkeep on these high volume swimming pools with having to replace popped off tiles, handrails and drain covers, and simply maintaining the equipment that runs these big pools.
When cities are faced with the burden and cost of major overhauls, like repairing structural cracking that causes heavy water loss, multitudes of options get thrown at them to make quick temporary repairs for pennies on the dollar, but most of those repairs are misguided and simply prolong the inevitable – which is how to repair those cracks permanently and leave a sound pool for years to come.
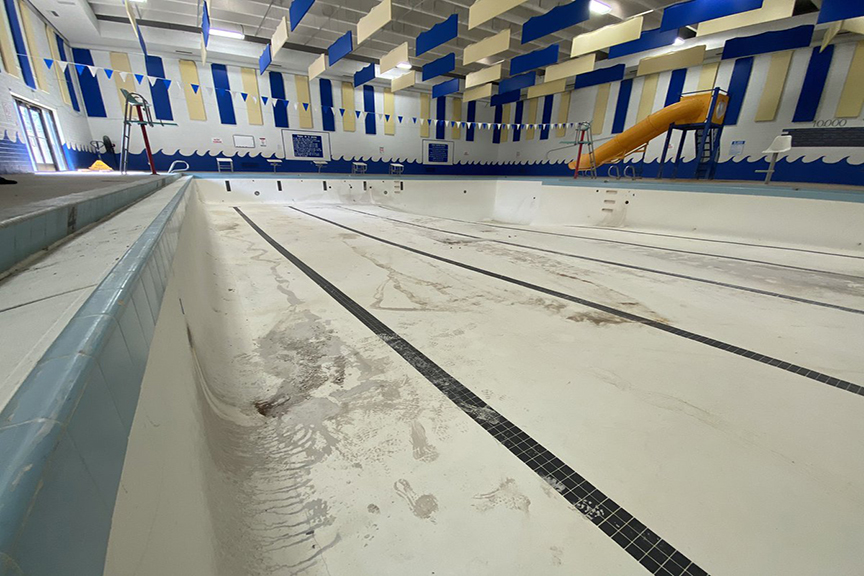
Almost every municipal pool we perform structural repair on suffers from the same previous and failed repair work. Epoxy injection is the most common, though there are times we see rebar pounded into the shell of the pool, rusting out as cracks widen. While these options may have stopped the water loss temporarily, ultimately the cracks continue to get bigger and water loss erodes the area where the crack first appeared and now the issue is even bigger.
It seems that most of the time, cities bring in engineers that survey the land the pool is on, review damage and discuss the same solution all the time. Demolish the pool and rebuild. Those engineer studies cost literally hundreds of thousands of dollars, on top of the thousands of dollars already put into failed repair missions in the past and in the end, the engineers don’t stand behind any claims on the pool – they just tell the city to demolish and rebuild.
This is ludicrous. Should the city and its taxpayers be on the hook for what will likely be more than a million dollars in rebuilding a pool when they’ve been given bad advice to start with? Unfortunately, communities around the country have drained pools that aren’t used because the cost is too high to rebuild and they’ve been convinced again and again that the solution is to throw money at the wrong ideas to find resolution.
The answer is, and was at the start, to install Torque Lock Structural Staples.
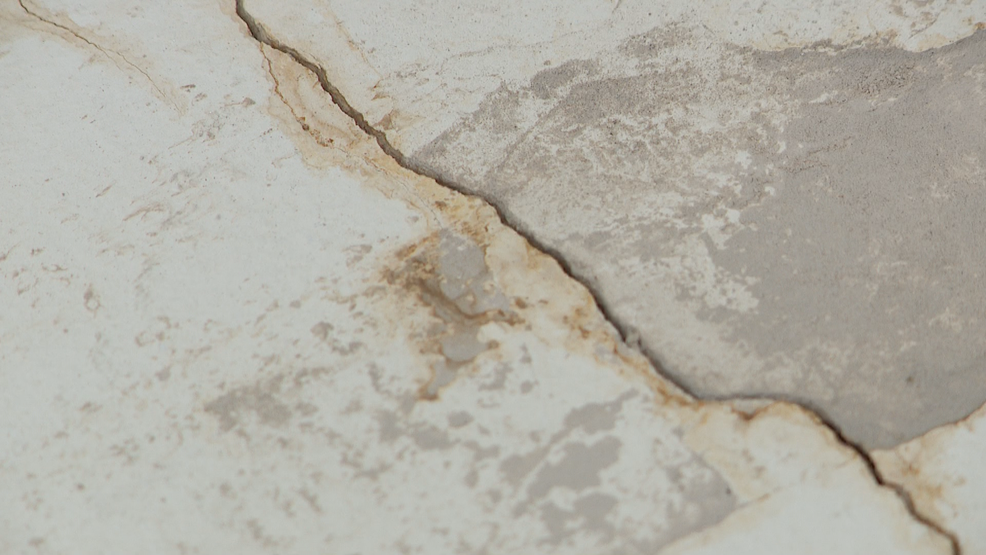
From the first sign of water loss due to structural cracking, the immediate action is to stop the crack and make repairs. For a pool repair contractor, the easy buck is to slather it up with some type of bubblegum and call it a day. The water loss stops, they get paid and by the time it starts to leak again in 6 months, they’re nowhere to be found.
Understand this: Epoxy injection is a temporary band-aid, not a permanent repair.
Epoxy injection does not fully penetrate cracks and leaves the damage open on the back side to continue its wrath. If it did fully penetrate the crack, it would still fail as concrete continued to shift. The crack was caused by forces that still exist, either ground movement, pressure behind a pool wall, settling or something that is forcing the two pieces of concrete apart. You aren’t resisting that pressure with epoxy injection. The epoxy is subject to drying, cracking and losing adhesion to the crack as those forces continue to widen and lengthen it. Now you simply have a bigger crack that leaks, with epoxy and other gathered junk inside of it.
Some contractors go the cheap route of pounding rebar into the pool shell, stating that this will keep crack from separating. We have decades of proof that it does not.
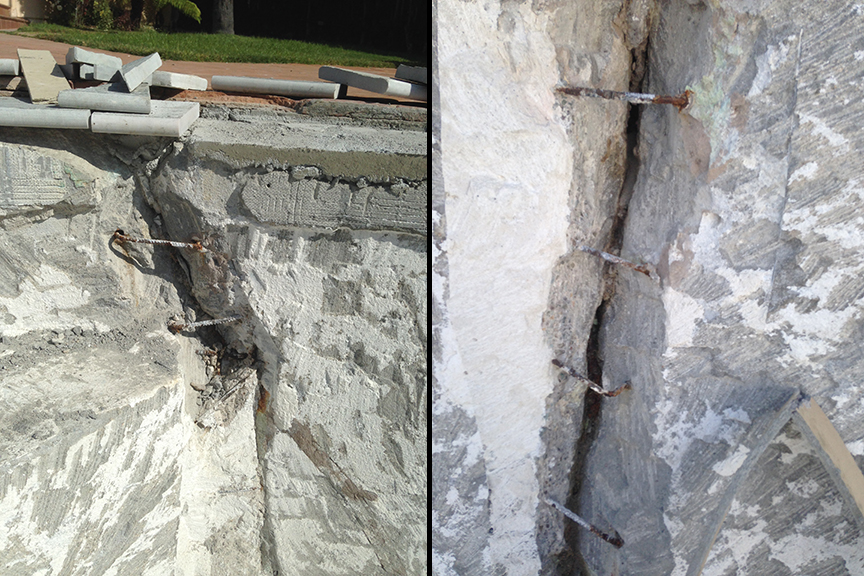
Rebar Failure – Every Time!
The reason being, it provides no resistance to cracking. While the idea looks sound, it lacks the one thing that is required to stop the crack altogether – and that is compression.
What’s worse is that some people have the delusion that using a combination of kevlar straps and epoxy will work. The theory is, epoxy alone won’t work, and flexible straps along do nothing, so of both are combined – simply gluing the fiberboard strip to the wall and putting epoxy over it might double up on the strength and keep the concrete from moving. It’s all on the surface and the concrete simply moves underneath it. You’d get the same result of you tried to fix the crack with scotch tape.
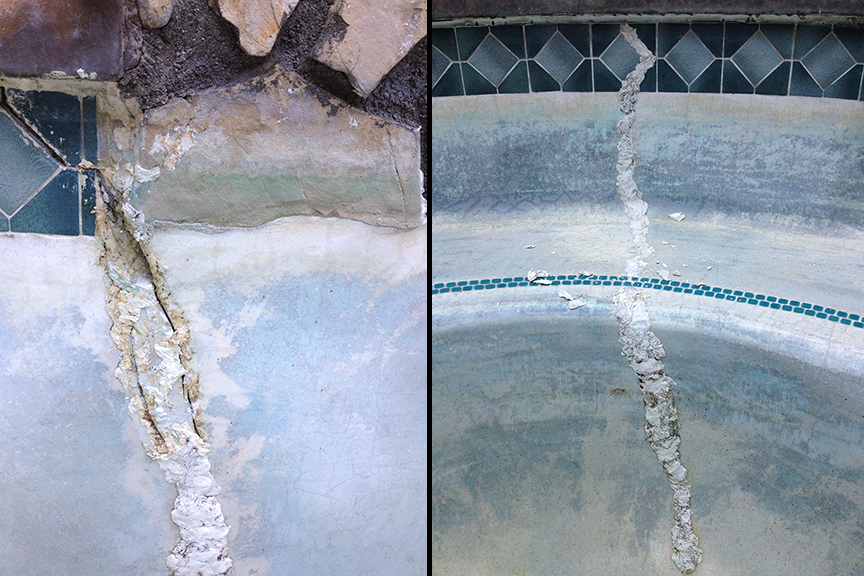
Epoxy Failure – Every Time!
For a cost hundreds of thousands of dollars below the price of even having a land engineer come out and misguide officials on ripping out a cherished community landmark, those cracks can be permanently repaired using Torque Lock Structural Staples.
Torque Lock Structural Staples and their method of installation are both patented; a proven method that when properly installed will end structural cracks permanently. For a price typically between $100 and $200 dollars per liner foot of crack repair when performed by an outside contractor and about $50 per linear foot when using in-house workers to make repairs – the solution cities need to reduce the heavy cost of repair and to keep their pool available to the community and as a revenue stream can be provided from the petty cash drawer in the office.
When installed, Torque Lock Staples span the gap of the crack and provide up to 5000 lbs of controlled compression to each side of the crack. This completely inhibits the cracks ability to widen, lengthen, re-crack, spread or shear. Rebar can’t do that!
The patented off-set cam that makes the Torque Lock Staple work rotates inward to provide this compression and is hand-tightened with a simple torque wrench, a $40 investment at any hardware store. Staples are installed at every 12 inch interval along the length of the crack and when finished over, the pool wall looks as new as the day it was first installed, without cracks and without water loss. The repair is permanent and the pool is set to last for decades to come.
Torque Lock was designed by Darren Merlob, a pool repair specialist who while working in the field, discovered that none of the available resources for structural crack repair provided adequate results. Every other repair method failed with time and had to be either re-applied or removed and rebuilt. With simple science and understanding of how cracks form, how they act and what they need to stop cracking – Merlob invented the staple that provided the required compression to end structural cracking forever.
On the official website, www.torque-lock.com, municipalities, homeowners, contractors and engineers can learn how Torque Lock Staples are properly installed and can have staple kits delivered directly to their door for immediate installation and repair on any solid concrete pool, spa or structure. This includes sea walls, solid concrete foundations, walkways and decking with a thickness of 4 inches or more and of course, concrete and Gunite pools and spas.
For more information on installation, purchasing or just to know more about the benefits of permanent structural crack repair using Torque Lock Staples, call 818-436-2953.